0. Introduction
In the paint manufacturing technology, the particle size and particle size distribution of the pigments and fillers used are very important indicators, which have a very important influence on the performance of the paint products. Large-scale instrument laser particle size analyzer can effectively carry out particle size analysis, and can quickly give test results, which brings convenience to paint developers. Laser particle size analyzer is an instrument with precise components and complex structure. When it is used, it is necessary to accurately set the condition parameters in order to obtain effective test results. The dry dispersion method uses compressed air as the dispersant to disperse the sample, which is suitable for the test of powder samples; the wet dispersion method uses the solvent as the dispersant, uses ultrasonic waves to disperse, and then generates a scattering signal by laser beam irradiation, which can be used For testing, you can also test emulsions and suspensions. Two test methods need to be selected according to the sample conditions [1].
1. Test Instruments
Germany Sympatec (Sympatec) company made HELOS / OASIS dry and wet two-in-one laser particle size analyzer, the test range is 0.1 ~ 875μm, install three lenses are: R1 (0.1 ~ 35μm); R3 (0.5 ~ 175μm); R5 (0.5 ~ 875μm).
2. Test principle
The working principle of laser particle size analyzer is based on light scattering theory and diffraction theory. When the light beam is projected onto the dispersion system of the instrument, light absorption, reflection, scattering, and diffraction can occur. When the frequency of the incident light is the same as the natural frequency of the molecule, light absorption occurs; when the wavelength of the incident light is smaller than the size of the dispersed particles, light reflection, diffraction, etc. occur; if the wavelength of the incident light is greater than the size of the dispersed phase particles At this time, light scattering occurs. Generally, for particles below 0.1μm, the diffraction phenomenon disappears, and the scattering phenomenon mainly occurs; particles with 0.1 ~ 10μm are also mainly diffracted light, and the particles will generate partial refraction and scattered light; particles larger than 10μm, both scattering and refraction disappear, Mainly diffraction. According to Fraunhofer diffraction theory, for particles of 10 μm, 0.1 to 10 μm, the size of the diffraction angle is related to the size of the particles, and the intensity of diffracted light is related to the number of particles, from which the size and number of particles can be determined. For particles below 0.1 μm and 0.1 to 10 μm, according to the Mie scattering theory, not only the diffraction of light but also the scattering and refraction of light are considered, and the calculation is based on the comprehensive refractive index of the particles to obtain the size and size of the particles [ 2].
3. Several important characterization parameters related to particle size analysis
X50: the corresponding particle size value when the cumulative distribution percentage reaches 50%, it is one of the important indicators reflecting the particle size characteristics of the powder. X50 is also called median diameter or median diameter. (X10, X90): indicates that particles smaller than X10 account for 10% of the total number of particles, and particles larger than X90 account for 10% of the total volume. The two features combine to indicate the range of sample particle size distribution. X (4,3): Represents the volume average particle size. The definition formula is: VMD = ΣniX4i / ΣniX3i. In general, its value is very close to X50, but it will also be significantly inconsistent if the particle size distribution is severely asymmetric. X (3, 2): represents the area average particle size, and the definition formula is: SMD = ΣniX3i / ΣniX2i, which is inversely proportional to the specific surface area in theory [3].
Note: The left coordinate in the figure is the cumulative distribution coordinate, and the right coordinate is the intensity distribution coordinate. All graph coordinates are the same.
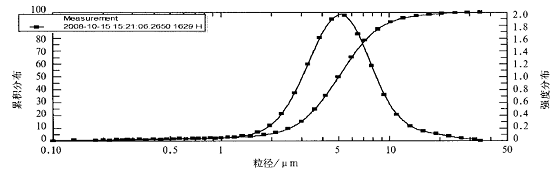
Figure 1 Zn powder dry dispersion method R1 lens test chart
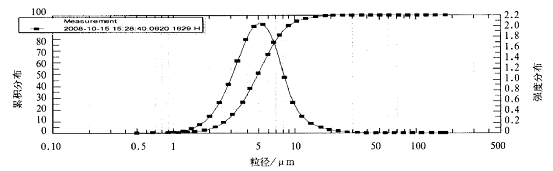
Figure 2 Zn powder dry dispersion method R3 lens test chart
Figure 3 Zn powder dry dispersion method R5 lens test chart
4. Test part
4.1 Determination of particle size and particle size distribution of zinc (Zn) powder by dry dispersion method
Measurement conditions: frequency of vibration tank 70%; pressure 0.4MPa; evaluation method: HRLD; test time: 10s. Choose R1, R3, R5 lens to test separately, the results are shown in Table 1.
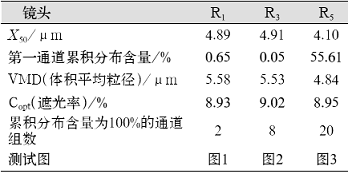
Table 1 Test results of Zn powder dry dispersion method
4.2 Wet dispersion method to determine the particle size and particle size distribution of zinc (Zn) powder
Dispersing medium: water; dispersing agent: sodium hexametaphosphate; stirring speed
Degree: 40%; ultrasonic dispersion time: 30s.
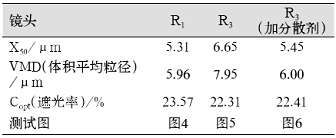
Table 2 Test results of wet dispersion method of Zn powder
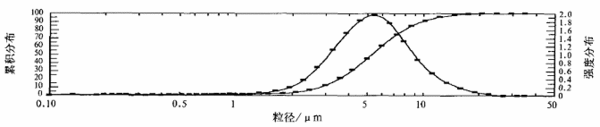
Figure 4 Zn powder wet dispersion method R1 lens test chart

Figure 5 Zn powder wet dispersion method R3 lens test chart
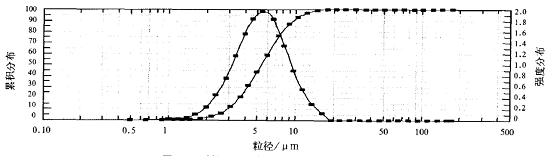
Figure 6 Zn powder wet dispersion method R3 lens adding dispersant test chart
5. Results and discussion
5.1 Discussion on test results of Zn powder
It can be seen from the test results of the dry dispersion method of Zn powder that different mirrors
There are some differences in the test results of the head. Although the sample particles are measured in the same area of ​​the lens, due to the different resolution of each lens, the resolution of the small lens is high, and the resolution of the large lens is low. It is difficult for the large lens to measure fine particles The diffracted light of the fine particles is detected, which causes an error in the analysis result. As shown in Table 1, X50 of R1 is 4.89 μm, X50 of R2 is 4.91 μm, and X50 of R5 is 4.10 μm. Because the test range of the R1 lens is 0.1 to 35 μm, the test range of the R3 lens is 0.5 to 175 μm, the test range of the R5 lens is 0.5 to 875 μm, and the test range of each lens is divided into 31 channels, the first channel of the R1 lens The resolution range is 0.1 ~ 0.18μm; the resolution range of the first channel of R3 lens is 0.50 ~ 0.90μm; the resolution range of the first channel of R5 lens is 0.50 ~ 4.50μm. Usually choose the appropriate lens to ensure that the cumulative particle distribution value of the first channel is less than 5%, and the cumulative particle distribution value of the first channel of the R5 lens given in Table 1 is as high as 55.61%, far exceeding the 5% The required value, so there will be serious deviations when using this lens, and many small particles of the sample will be missed, and the test results will have a small error value. It can also be seen from Table 1 that the cumulative distribution content is 100% of the number of channel groups, R1 is 2 groups, R3 is 8 groups, and R5 is 20 groups. Generally, a suitable lens is also a suitable range, and the cumulative distribution content of the sample The number of channel groups that reach 100% should be guaranteed to be about 4 groups. It can be seen from the analysis that the R3 lens is more suitable for this Zn powder sample. From the test chart of the wet dispersion method of Zn powder, the test result of the wet dispersion method is larger than that of the dry dispersion method, which is the test difference brought about by using different dispersion methods. Similarly, the test result of the sodium hexametaphosphate without the dispersant in the wet dispersion method test is also larger than the test result after the addition of sodium hexametaphosphate. The choice between the dry dispersion method and the wet dispersion method depends on the specific sample conditions. The dry dispersion method is convenient and fast, but the dispersion system of the dry dispersion method uses air flow to disperse the sample particles. Due to the friction between the molecules of the sample, an electrostatic force will be generated, which will cause the sample particles to reunite. If the selected pressure is low It will cause uneven dispersion of the sample in the dispersion tube, causing test errors, and at the same time the sample consumption during the dry dispersion test is relatively large. Compared with the dry dispersion method, the wet dispersion method can use ultrasound and a suitable dispersant to disperse the sample. The method is flexible and diverse, and the amount of sample is less. The disadvantage is that the dispersion medium must be accurate. Furthermore, the state of the sample to be tested also determines which test method should be selected. For example, some easily soluble pigment particles must be tested using the dry dispersion method, and the resin emulsion must use the wet dispersion method. For many samples, it is necessary to add a dispersant to the dispersion medium, otherwise the dispersion cannot be performed sufficiently. After adding a small amount of dispersant in the dispersion medium, the positive or negative ions of the dispersant will be adsorbed on the surface of the sample particles, thereby generating hydration and making the particles repel each other. When the repulsive force is greater than the van der Gravity force between the particles, the particles will maintain a good dispersion state [4], so after adding surfactants such as sodium hexametaphosphate, the particles are in a good dispersion state, so that the test results The results of the previous test of the surfactant are reduced.
5.2 Discussion of test methods
5.2.1 Discussion of dry dispersion test methods
The steps of the dry dispersion method test are generally to set the test conditions of the sample on the software operation interface of the instrument, and then start the background test button. The system will test the optical state of the instrument lens and the cleaning of the pipeline without adding a sample. Status, and then give the background value, usually the background value is not higher than 5. If the background value of the test is relatively large, you can wipe the lens with a cotton ball dipped in alcohol or remove the dirt particles in the pipeline by starting the exhaust system device. After the background test is normal, you can sample it for testing. The dry dispersion method is to use compressed air to disperse the sample. It is necessary to ensure that the sample particles will not be broken and can be well dispersed. At the same time, the amount of the sample taken is also representative, so special attention should be paid to the selection of dry dispersion method test conditions The key parameters such as the pressure of the air and the size of the shading rate should also be set according to the characteristics of the sample, the injection rate, the height of the vibration tank, and the initial conditions of the test. The shading rate reflects how many samples are in the laser beam during each test, and its value is not only related to the shape and composition of the sample, but also proportional to the number of samples. Therefore, the amount of sample required for the test needs to be adjusted according to the value of the shading rate. The required amount must not only avoid multiple scattering, but also avoid insufficient signal. Usually the shading value is controlled below 15%, the best is 7% ~ 10%.
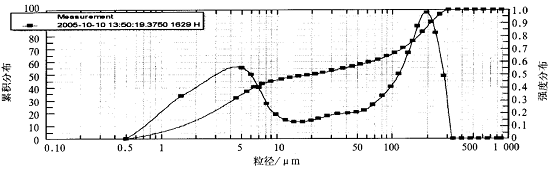
Figure 7 iron oxide red test chart
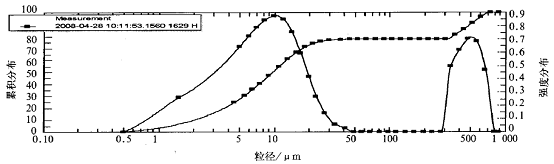
Figure 8 Titanium dioxide test chart
Pigment particles with high density and fine particle size such as titanium white and iron oxide used in coatings are very prone to agglomeration due to the effect of electrostatic force. Generally, a pressure of 0.3 MPa or more is required to effectively disperse the sample. Below a pressure of 0.3 MPa, the sample cannot be effectively dispersed. When the red pigment iron oxide was tested with a pressure of 0.1 MPa and a rate of 60%, a double peak appeared on the distribution map, with a high tail peak, indicating that a large number of particles were agglomerated together and failed to disperse, as shown in Figure 7 . White pigment titanium white, using 0.1MPa pressure, 60% of the rate will also appear the phenomenon of large particle aggregation, as shown in Figure 8. Therefore, the set dispersion pressure is different for different samples due to different density and particle thickness. Usually, the minimum dispersion pressure is used under the premise of ensuring good dispersion, which can not only disperse the sample, but also protect the dispersion tube of the instrument and extend the life of the dispersion tube.
5.2.2 Discussion of wet dispersion test methods
To use the wet dispersion method for testing, first set the wet dispersion method as the current test method, then the device will automatically switch from the dry dispersion method to the wet dispersion method. Then set the test conditions of the wet dispersion method, such as peristaltic pump speed, ultrasonic rate, time, stirring speed, etc., and then start the start button to conduct a background test. If the background is high, you need to clean the lens, flush the pipeline, etc., to ensure that the background value is relatively low, and then add the sample. Control the amount of sample added to keep the shading rate within a certain range. The shading rate range can be selected from 5% to 30%, preferably 20% to 30% [5]. After the sample test, the software will give the results in the form of a graph.
The conditions for selecting the dispersion medium by the wet dispersion method are generally: ①It is in a transparent state so that the laser can pass through; ② It can be used with the material of the instrument without dissolving or changing the particle size of the sample; of. ④ Sample particles can be dispersed easily and stably. ⑤ The refractive index differs greatly from the sample particles. ⑥ It can be circulated with proper viscosity. Generally, water is used as the dispersion medium in the test, and low-foam surfactants are added to reduce the surface tension of the water. Ethanol, isopropanol, hexane, or isooctane can also be used as the dispersion medium according to the sample and instrument conditions 6].
Pigments used in coatings such as titanium white, iron oxide, calcium carbonate, kaolin, etc., the refractive index is generally 2.50, 2.60, 2.42, 1.52, 1.61, etc., and the refractive index of water is about 1.33, usually added surfactant Later, it can be used as a dispersion medium for these samples. Appropriate ultrasonic time and intensity can give the dispersed sample appropriate energy, which is conducive to the dispersion of the dispersed sample particles to form a stable and uniform dispersion solution. Ultrasonic power is too large or time is too long to easily lead to sample rupture, so the use of ultrasonic time and power increase selection test, observe the final particle size test chart, the particle size distribution in the figure is stable and no longer decreases when the time and intensity settings Is the last value. Generally, the setting range of the stirring rate is 1% to 100%. When the rate is 100%, the power is 60W. After stirring, the emulsion is easy to bring in bubbles, causing errors, which will affect the measurement results. As shown in Figure 9, a protruding peak appears at the tail, which is caused by the introduction of bubbles after stirring. Therefore, the emulsion test, the stirring rate should not be too high, preferably 20% to 50%.
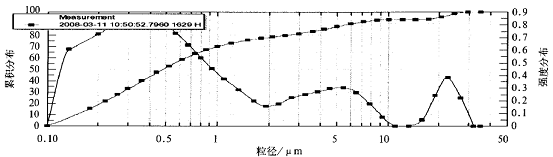
Figure 9 emulsion particle size test chart
6. Conclusion
The laser particle size analyzer can accurately determine the particle size and particle size distribution of pigments, fillers, emulsions, powder coatings, etc., and it is more convenient to choose dry dispersion measurement or wet dispersion measurement. Both can objectively reflect the particle size distribution of the sample. Regardless of whether the wet dispersion method or the dry dispersion method is used, in order to ensure the accuracy of the test results, it can be known from the above discussion that the following points should be achieved: (1) The appropriate dispersion pressure should be selected for the dry dispersion method test. The size of the pressure can completely disperse the added sample particles in order to measure the accurate sample particle size distribution, otherwise the test result is only the particle size distribution of the sample agglomerated particles, and it cannot meet the test repeatability requirements of the sample. (2) The selection of the dispersion medium and dispersant by the wet dispersion method is very important. Only by selecting the appropriate dispersion medium and dispersant according to the characteristics of the sample can an accurate sample particle size distribution be obtained. (3) The lens under test cannot be contaminated, the lens must be kept clean, so as to ensure the accuracy of the test results. (4) The shading index is controlled within an appropriate range. The dry dispersion method test is controlled at 7% -10%, and the wet dispersion method test is controlled at 20% -30% as the best test range.
The living room is the first space guests see when they enter your home, and it's the area where they spend most of time. Therefore, our living room should be designed as an ideal place for entertainment and relaxation, which is comfortable, bright and beautiful. A suitable combination of different living room furniture can embellish your living room and make the whole space full of vitality.
Living Room Furniture,modern living room furniture,luxury living room furniture,minimalist living room furniture
Foshan Poesy Furniture Co., LTD. , https://www.poesyfurniture.com